CCM Manufacturing
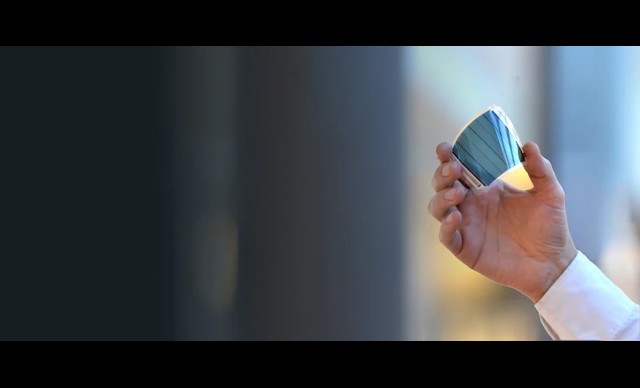
19 September 2023
The CCM is crucial in fuel cells, facilitating electrochemical reactions, proton flow, and electricity generation while ensuring water is produced. Designing and making the CCM right is vital for fuel cell efficiency and performance.
Coating a CCM (Catalyst-Coated Membrane) in a fuel cell is a delicate process that requires careful consideration of several factors to ensure optimal performance and reliability. Here are some key aspects to be aware of when coating a CCM:
1. Uniformity: Achieving a uniform coating on the membrane is critical to ensure consistent electrochemical reactions across its surface. Non-uniform coatings can lead to localized variations in performance.
2. Catalyst Loading: The amount of catalyst (typically platinum nanoparticles) applied to the CCM must be carefully controlled. Too much or too little catalyst can impact the fuel cell's efficiency and durability.
3. Catalyst Distribution: Ensure that the catalyst is evenly distributed across the membrane to promote even reaction kinetics. Clustering of catalyst particles should be avoided.
4. Thickness Control: The thickness of the catalyst layer should be controlled precisely. Too thick a layer can increase mass transport resistance, while a very thin layer might not provide sufficient catalytic activity.
5. Adhesion: Proper adhesion of the catalyst layer to the membrane is crucial to prevent delamination during fuel cell operation. Adhesion promoters or techniques should be considered.
6. Porosity: The catalyst layer should have the right level of porosity to facilitate the diffusion of reactants (e.g., hydrogen and oxygen) to the catalyst sites. Excessive porosity can lead to reduced catalyst utilization.
7. Compatibility: Ensure that the materials used in the coating process are chemically compatible with the CCM and do not degrade the membrane's proton-conducting properties.
8. Drying and Curing: Proper drying and curing processes are essential to eliminate solvents and to bond the catalyst securely to the membrane. Insufficient drying or curing can lead to defects.
9. Quality Control: Implement quality control measures to monitor the coating process, such as thickness measurement, catalyst loading analysis, and adhesion testing.
10. Environmental Factors: Consider the environmental conditions, such as temperature and humidity, as they can affect the coating process and the quality of the CCM.
11. Scaling Up: If you are scaling up production, ensure that the coating process is scalable and can maintain consistency across a larger volume of CCMs.
12. Safety: Be aware of safety precautions when working with chemicals, solvents, and materials used in the coating process.
13. Testing and Characterization: After coating, conduct thorough testing and characterization of the CCMs to verify their performance, such as electrochemical testing and durability testing.
Coating a CCM in a fuel cell is a critical step in manufacturing, and attention to these factors can contribute to the overall efficiency and longevity of the fuel cell.